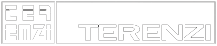

KitMe: un progetto nel quale TERENZI SRL ha supportato con la tecnologia al fine di ingegnerizzare gli stampi e produrre le parti estetiche del primo servizio sviluppato.
Disegnato da Design Group Italia, con progettazione elettronica di DAOS Group, è una soluzione composta da uno smartwatch e sensori universali. L’innovativo sistema si fonda sulla rilevazione in tempo reale di qualsiasi fonte sonora o vibrante diffusa nell’ambiente che ci circonda. Al kit si abbinano un’App e un servizio clienti accessibile che, essendo composto da personale sia sordo che udente, è in grado di rispondere a qualsiasi esigenza comunicativa. IntendiMe mette a disposizione qualcosa di unico nel suo genere, associato a un kit che consente la rilevazione dei suoni e delle vibrazioni. KitMe è creato “con i sordi per i sordi” e – non solo - eroga un controllo di assistenza tramite chat e videochat anche in LIS (Lingua dei Segni Italiana) con operatori sordi e udenti.
Il kit funziona con una comunicazione radio proprietaria e con Bluetooth (per la configurazione), ha un’ampia copertura del segnale: non è quindi necessario disporre di una rete internet o una rete elettrica. A ciò si aggiungono l’assenza di interferenze sonore e le dimensioni ridotte da cui derivano quindi versatilità e trasportabilità: KitMe si può spostare ovunque sia in termini di luogo (casa, lavoro, vacanza...) che in termini di fonte rilevabile (qualsiasi fonte vibrante e/o sonora). Ha inoltre un’estetica di design curata e funzionale, non è un dispositivo medico ma un accessorio alla portata di tutti. Il design, lo studio di fattibilità, l’ingegnerizzazione e poi la filiera produttiva progettata ad hoc hanno reso concreta l’idea iniziale e fattibile di un prodotto complesso. È un progetto sociale, dunque, ma anche funzionale ed estetico che ruota intorno al concetto di ergonomia.
Nel progetto, TERENZI SRL è stata coinvolta per quanto riguarda l’industrializzazione del prodotto, per individuare e proporre soluzioni sui materiali da impiegare, sulle tecnologie esecutive e sulla fattibilità dal punto di vista meccanico. Si è deciso di realizzare degli stampi a iniezione con movimenti idraulici per la produzione delle parti in plastica, e parliamo in questo caso di sei stampi, uno per le guide LED e i tasti di smartwatch e sensore, gli altri cinque rispettivamente per la cassa del sensore, il caricabatterie, il cinturino, la cassa dello smartwatch e la sua cornice. Nello stampo per l’esecuzione di smartwatch e sensore si ottiene anche il sovrastampaggio “plastica su metallo” che incorpora i 4 pogo pin connector. Lo stampo riguardante la cassa dello smartwatch è stato appositamente ideato per il tipo di materiale in questione, cioè l’ABS; tale stampo è in acciaio 1730 con tasselli e matrici in acciaio 2085. La fase di stampaggio dei sensori avviene mediante “iniezione sottomarina” che consente la divisione automatica dei pezzi dallo sfrido.
Il prodotto è composto nel suo insieme da tre sensori che si applicano sulle fonti sonore e da uno smartwatch che notifica in tempo reale le rilevazioni; inoltre è presente un’App per gestire i sensori e le altre funzioni dello smartwatch contemporaneamente.